Introduction
The fundamental pillars of prosperous industrial operations encompass efficiency, productivity, and orderliness. In the realm of manufacturing, the optimization of processes and the minimization of waste are crucial factors in maintaining competitiveness. The 5S approaches are implemented in this context. The 5S methodology, which originated in Japan, is a systematic approach to organizing the workplace. It encompasses five key principles: sort, set in order, shine, standardize, and sustain. This article aims to examine the 5S techniques in manufacturing and analyze their use as a means for firms to enhance operational efficiency and quality.
Seiri
The concept of sorting, also known as seiri in the context of lean manufacturing, refers to the process of organizing and categorizing
The letter “S” stands for the first component of the 5S framework, which is also known as “Sort” or “Seiri” in Japanese. This stage entails the process of categorizing and evaluating all the items present within the workplace, distinguishing between essential and non-essential goods. Superfluous items encompass a wide range of objects, such as tools, equipment, supplies, and records.
Implementation
The objective is to streamline the workplace by retaining only the necessary items relevant to the ongoing tasks.
- The execution or application of a plan, method, or system
- Perform a comprehensive evaluation of the working environment.
- Eliminate all superfluous things and resources.
It is imperative to ensure that goods are appropriately labeled and categorized in order to facilitate their simple identification.
Benefits
There are several advantages to consider.
- The presence of minimal clutter and distractions.
- Optimizing spatial utilization.
- Enhanced safety measures

The concept of “Set in Order” (Seiton)
In the context of organizational management, the letter “S” stands for the second principle, also known as “Set in Order” or “Seiton.” After categorizing the essential components, the subsequent task involves arranging them in a coherent and systematic fashion. The primary goal is to enhance the accessibility of necessary resources for employees, thereby diminishing the duration of search efforts and mitigating the potential for mistakes.
Implementation
- The execution or application of a plan, method, or system
- Allocate distinct positions for each individual item.
- One effective approach to organizing and storing items is to employ explicit storage solutions, such as shelves, racks, and containers.
- Design visual indicators or symbols to facilitate quick and effortless recognition.
Benefits
There are several advantages to consider.
- The duration of search processes has decreased.
- Enhanced operational efficiency and increased output.
- The implementation of organized storage systems leads to an improvement in safety measures.
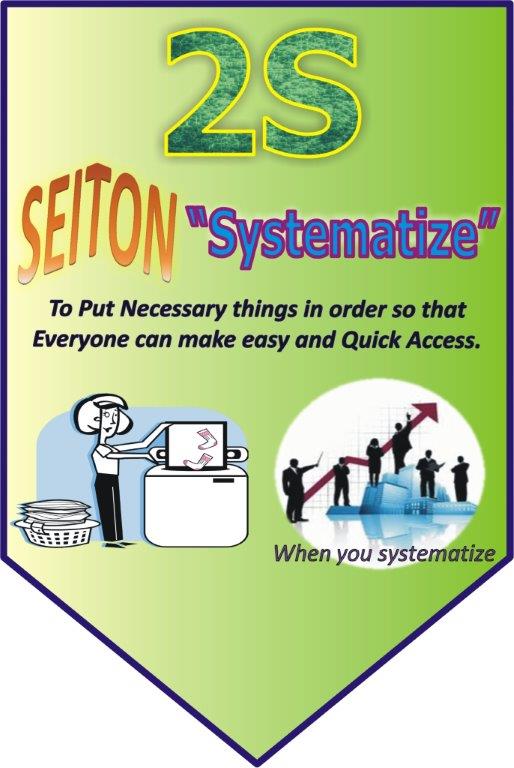
Seiso
The concept of “shine” (Seiso) refers to a state of brightness or radiance.
The third “S” represents the concepts of “shine” or “seiso.” This stage entails the process of tidying up the work area and ensuring that all equipment is properly cleaned. The presence of a clean environment not only serves to improve the visual appeal but also plays a significant role in promoting workplace safety. The use of routine cleaning and maintenance procedures serves to mitigate the occurrence of equipment malfunctions and enhance overall operational efficiency.
The execution or application of a plan, method, or system
Implementation
- Implementing a structured cleaning regimen and allocating certain duties
- It is advisable to allocate resources towards the acquisition of suitable cleaning tools and supplies.
- It is imperative to foster a culture of cleanliness among employees, particularly in their respective work areas.
Benefits
There are several advantages associated with this phenomenon.
- Enhanced durability of equipment
- Increased employee morale.
- Reduced incidence of accidents.
- The concept of standardization, also known as Seiketsu, is a fundamental principle in various fields, including manufacturing and quality.
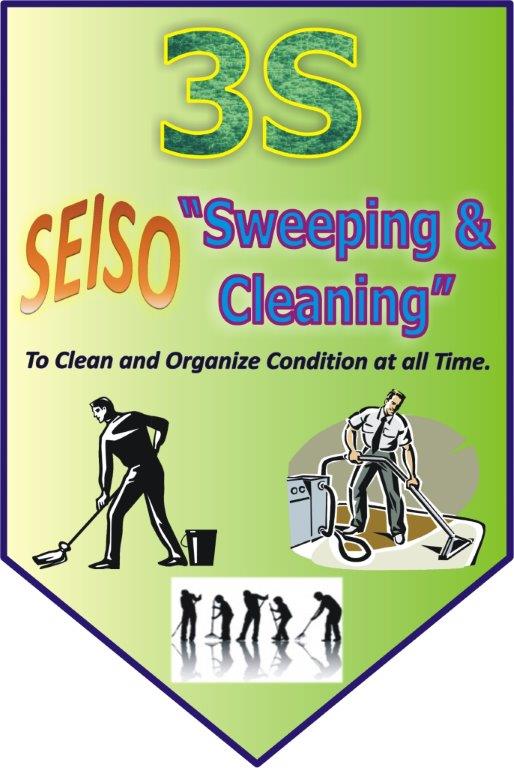
Seiketsu
The fourth element of the 5S approach is known as “standardize” or “seiketsu.” During this phase, standards and procedures are established and implemented to govern operations within the workplace. Standardization plays a pivotal role in promoting uniformity across individuals, fostering heightened levels of efficiency and quality.
Implementation
- The execution or application of a plan, method, or system
- The objective is to establish work practices that are both clear and straightforward.
- Record the precise whereabouts of tools, materials, and equipment.
- Provide training to staff regarding the specified criteria.
Benefits
- There are several advantages to consider.
- The concept of consistency in operations refers to the practice of maintaining uniformity and stability in various aspects of an organization’s activities.
- The objective is to minimize errors and discrepancies.
- Facilitating a smoother and more efficient process for integrating new personnel into an organization
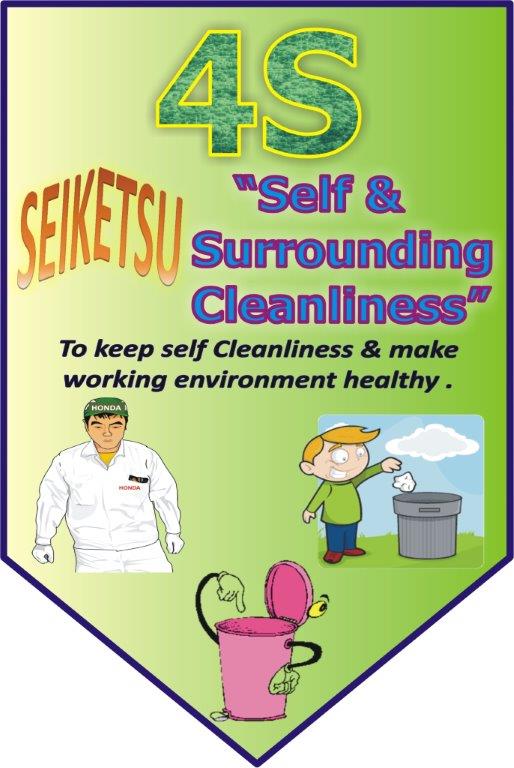
Shitsuke
The concept of sustainability, known as shitsuke in Japanese, refers to the practice of maintaining and continuously improving established standards and processes.
The fifth and ultimate “S” is referred to as “Sustain” or “Shitsuke” in the context being discussed. The process of maintaining the 5S system involves integrating it into the cultural fabric of the company. Sustained dedication, attentiveness, and enhancement are necessary. The implementation of regular audits, feedback mechanisms, and reinforcement strategies plays a pivotal role in ensuring sustained success in adhering to the 5S principles.
Implementation
- The execution or application of a plan, method, or system
- It is recommended to perform routine 5S audits.
- Offer continuous training and support.
- Promote and foster employee engagement and accountability in the implementation of the 5S process.
Benefits
There are several advantages associated with this phenomenon.
- Continuous enhancements.
- Improvement of organizational culture inside the workplace
- The achievement of long-term improvements in efficiency and quality

Conclusion
In conclusion, it can be inferred that the given information leads to the stated conclusion.
The utilization of the 5S approaches in the manufacturing industry offers a methodical and structured approach to enhancing workplace organization and optimizing operational efficiency. Manufacturing businesses can achieve waste reduction, efficiency enhancement, safety improvement, and consistent quality standards by adopting the principles of sort, set in order, shine, standardize, and sustain. The 5S technique is characterized by its continuous nature, as it is not limited to a singular occurrence but rather an ongoing process. When well integrated into the organizational culture, this methodology has the potential to yield enduring achievements in industrial processes.