Introduction
The PDCA cycle (Plan-Do-Check-Action) is a method for routinely enhancing production procedures. It has four steps that help businesses find ways to improve their performance and efficiency. In our daily work, the methods that are determined to be appropriate
The PDCA Cycle: An Explanation
The Plan-Do-Check-Action (PDCA) cycle is a structured approach to problem-solving that emphasizes constant advancement in production. It is also known as the Deming cycle and the Shewhart cycle. After Walter A. Shewhart first proposed it in the 1920s, Dr. W. Edwards Deming, a leading expert on quality management, popularized it.
The Value of the PDCA Cycle to Factory Productivity
Organizations that want to maximize manufacturing efficiency should use the PDCA cycle. By taking a methodical approach to solving problems and improving performance, businesses may cut down on inefficiency and boost output.
Four Stages of PDCA
Plan: Establishing Objectives
Organizations develop industrial improvement targets and outline objectives to drive efficiency in the planning phase of the PDCA cycle. The first step is to pinpoint the specific areas of the manufacturing process that need the most attention.
- Creating goals that can be tracked and evaluated and that contribute to the larger goals of the company
- Establishing metrics by which success can be gauged and progress monitored
DO: Executing Improvement Strategies
In the “do” phase, you’ll implement in action the plans for growth that you developed in the “plan” phase. This involves: • Implementing adjustments to the production procedure to address the identified weak spots.
- Making smart use of available assets to facilitate the realization of enhancement strategies
- Getting input from workers at all levels is necessary to guarantee support and cooperation.
Check: Monitoring Progress and Analyzing Results
The “check” phase involves checking in on the development of the modifications made and reviewing the outcomes. This phase involves:
- Comparing actual results to the predetermined standards of performance and key performance indicators
- Data analysis to pinpoint problem spots or places for development.
- Analyzing how the new procedures have improved production efficiency.
Action: Verify that there are no problems.
Taking corrective measures based on the findings from the preceding phases constitutes the “action” step. This entails, among other things:
- Locating spots in need of tweaks or upgrades
- Modifying production procedures or methods as required
- To maintain consistency and longevity, successful processes should be standardized.
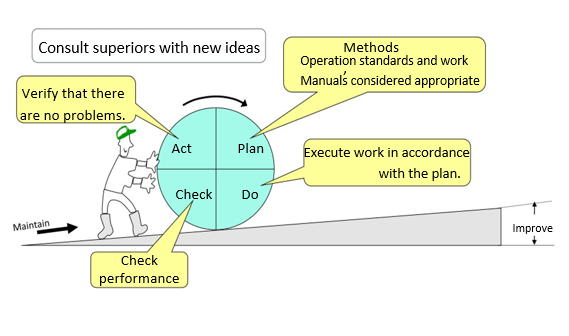
Implementing the PDCA Cycle in Manufacturing
Creating a Habit of Constant Refinement
Organizational cultures that encourage constant tweaking and refinement are crucial for effective PDCA cycle implementation in manufacturing. To achieve this goal, it is necessary to:
- Encourage an attitude that values creativity and the pursuit of new solutions.
- Inspiring workers to use their own initiative and originality in seeking out areas for growth.
- Fostering a culture that encourages risk-taking and recognizes the importance of mistakes as stepping stones to success
Stakeholder Engagement and Collaboration
The active involvement of stakeholders is crucial for the effective execution of the Plan-Do-Check-Act (PDCA) cycle. This is the practice of engaging workers at various hierarchical levels within the business, acknowledging and appreciating their valuable perspectives and efforts.
- One strategy to foster cooperation and information sharing is the establishment of cross-functional improvement teams.
- One way to foster a culture of improvement is by promoting open communication and encouraging active engagement in the improvement process.
Selecting Appropriate Tools and Techniques
In order to optimize the efficacy of the Plan-Do-Check-Action (PDCA) cycle, it is imperative for businesses to employ pertinent tools and procedures.
- This entails the utilization of statistical process control (SPC) methodologies for the purpose of monitoring and controlling industrial processes.
- The use of Lean Manufacturing concepts, such as the utilization of value stream mapping and the adoption of the 5S approach, with the aim of eradicating inefficiencies and optimizing productivity.
Case Studies: PDCA Cycle Success Stories
The PDCA Cycle in the Toyota Production System
Toyota’s production system is often cited as an example of the successful use of the PDCA cycle. Toyota’s impressive gains in manufacturing efficiency can be attributed in large part to the company’s adoption of the Plan-Do-Check-Action (PDCA) cycle. This cycle forms the backbone of Toyota’s quality management system and encourages employees to identify and address inefficiencies.
Potential Barriers and Pitfalls in PDCA Implementation
Lack of leadership support and commitment
Lack of buy-in from upper management is a typical impediment to a smooth PDCA rollout. The key to overcoming this obstacle is for leaders to be seen as change agents and providers of the resources needed to implement such changes.
- Sharing the PDCA cycle’s value with upper management requires explaining its merits.
- To show their dedication, leaders should take part in the process of improvement.
Inadequate data collection and analysis
For PDCA to work, it is crucial to gather and analyze data in an efficient manner. Overcoming obstacles in data collection, such as ensuring data quality and dependability, is essential to tackling this problem.
- Using effective methods of data management, such as graphical representations of data and statistical evaluations,
- Spending money on equipment and human resources to facilitate data gathering and analysis.
Benefits and Impact on Manufacturing Efficiency
Enhanced Process Optimization and Standardization
Improved process optimization and standardization are the results of incorporating the PDCA cycle into production. By doing things like:
- Creating streamlined and repeatable procedures that decrease variability
- Adopting standard procedures company-wide to boost productivity.
Manufacturing practices that improve overall productivity and decrease waste
Improved quality control and defect reduction
Organizations may enhance quality control and decrease defects by using the PDCA cycle, which involves:
- Locating and removing the causes of faults during production
- Taking precautions to reduce the occurrence of errors and maintaining high-quality standards
- Improving the quality of our products and services as a whole
Increased employee engagement and empowerment
A system of employee involvement and empowerment may be fostered through PDCA implementation by doing the following:
- Encouraging workers to take ownership of their work and provide recommendations for changes.
- Offering chances to learn new things and improve existing ones.
- Fostering a culture of loyalty and pride among employees
Conclusion
The PDCA cycle provides a robust methodology for boosting production effectiveness. The optimization of processes, the development of quality, and the empowerment of the workforce are all areas in which businesses may make substantial strides by methodically addressing areas for improvement, engaging people, and using suitable tools and methodologies.