The “5 Whys” is a technique of solving problems that is frequently used in manufacturing and other industries to identify the origins of issues. It is a simple technique that entails constantly asking “Why?” until the root cause of a problem is identified. Instead of only treating a problem’s symptoms, the goal is to find its underlying cause.
Investigating the Root Causes: Problems including product flaws, equipment failures, and production delays are frequent occurrences in the manufacturing industry. The key to a successful resolution of these issues is locating their underlying causes. By using a “Why-Why” analysis, you can expose the fundamental causes of a problem by removing the various layers of dependency.
Preventing Recurrence: Recurrence can be avoided by addressing the fundamental causes of the issue. You can put into place long-lasting remedies, enhancing product quality, production effectiveness, and general dependability, by addressing the fundamental problems. The price of quality control and rework is decreased by this proactive strategy.
Cost reduction: Problems and errors in the production process can be expensive. By identifying the underlying causes of problems you may implement targeted adjustments that cut down on waste, rework, and the demand for costly, last-minute remedies. In the end, this results in cost reductions and elevated profitability.
System Optimization: Continuous improvement approaches like Lean and Six Sigma are intimately related to Why-Why analysis. It aids manufacturers in optimizing their procedures, enhancing their reliability and effectiveness. You can pinpoint opportunities for process standardization and improvement using this investigation. Making decisions based on data is becoming more common in manufacturing. Data and facts are used in the Why-Why analysis to pinpoint the main causes. It promotes a process of choice process that is grounded in facts, which is essential for contemporary manufacturing processes.
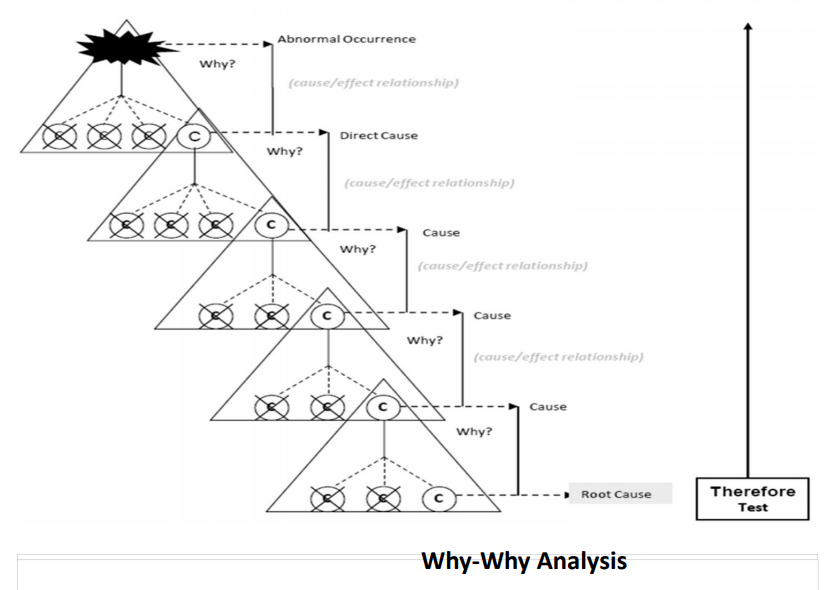
In conclusion, The “5 Whys” technique is beneficial since it improves in avoiding temporary measures that merely treat symptoms and instead focuses on resolving the root causes of the issue to stop it from happening again. It helps in decreasing expenses, improving workflows, and raising product quality.